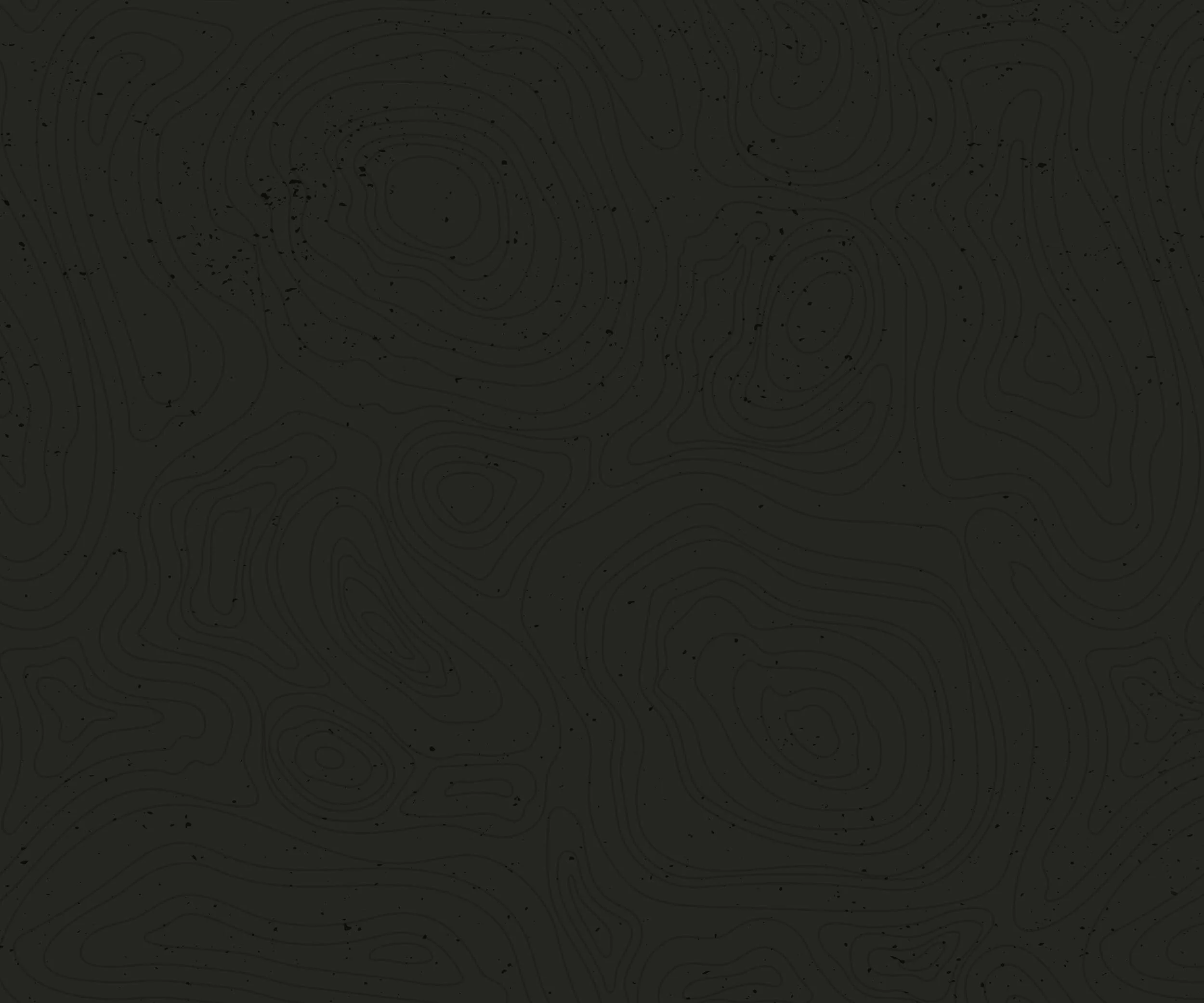
ModOuts Solutions
Temporary Housing
More Than a Shelter
At ModOuts, we believe in providing more than just shelter; we offer a dignified and sustainable solution for those in need. Our innovative homeless shelter villages are designed to create a safe, comfortable, and supportive environment. Each unit is thoughtfully crafted with high-quality materials and practical design, ensuring a place where individuals and families can regain stability and hope. Join us in transforming lives and communities, one village at a time.
Why Choose ModOuts?
Emergency housing with the quality of permanent construction
DIGNITY LIVING
Shelters that look and feel like a real home. No metal or fiberglass sheds but real drywall, fiber-cement siding, and insulation for comfortable living. A solid core entry door with key-pad lock and dual-pane residential windows offer a safe living experience.
EASY REDEPLOYMENT
Once a project comes to an end, all units can be easily transported to be re-used. Potential damage through intense use can be easily repaired by standard methods (paint and drywall touch-up). This allows ModOuts shelters to provide long lasting value.
DURABLE CONSTRUCTION
94% of homes in the US are wood framed. It’s the most proven and time tested construction method. Why settle for less? Fiber cement siding comes with a 50 year life expectancy, roofing shingles between 20-30 years. ModOuts are build to last, be redeployed multiple times and keep maintenance expenses low.
PROJECT SIMPLICITY
Since our company history started 15 years ago as a turn-key design-build construction company, the US-Offsite and ModOuts team is able to offer a one-stop solution starting at design, and engineering over to site-prep, manufacturing, and install of a complete shelter village. Our team is able to perform all steps necessary to complete a successful project or to consult the existing team on all scopes that are performed by others.
FLEXIBLE DESIGN
Even though we offer pre-engineered solutions, we are aware that emergency shelters are new to most local jurisdictions, planning, and building departments. While Appendix P brings some clarity and guideline, it still leaves room for specific local requirements that make it challenging for standardized products to meet all specifications in regards to fire and life safety, size and accessibility. Our experienced design team will be able to adjust our standard plans to meet all local requirements and support through the whole permitting process.
General Specifications
Appendix P Compliance
All units comply with Appendix P requirements:
Unit Sizes
Heater and AC
Structurally Engineered
Egress
-
• Standard: 2x4 walls with R13 Insulation
• Upgrade: 2x6 walls with R21 Insulation
• 2x6 floor with R30 Insulation
• Trussed roof with R30 insulation
-
• Windows white vinyl Milgard V250 or similar
• Durable solid core fiberglass exterior doors
• Solid core wood interior doors for reduced noise transmission
-
• All plumbing fixtures to be low-flow water conserving Delta/American Standard or similar
• ADA compliant plumbing fixtures in all ADA units
-
• Recessed can lights on dimmer
• One exterior sconce per exterior door for improved safety
• One smoke and CO2 detector combo unit per sleeping room
• Minimum one outlet per wall
• All circuits AFCI/GFCI protected
• One panel per living unit
-
• Standard: minimum 8k BTU combined Heating and Cooling through the wall AC
• Upgrade: PTAC system
• Upgrade: Mini-Split system
-
• Fibercement Siding
• Asphalt Shingle Roof (30 year shingle)
• 1/2” drywall with orange peel texture
-
• Standard: 50 mil sheet vinyl flooring
• Upgrade: LVP flooring
• lockset with digital keypad
-
• Standard: All permanently attached fixtures, finishes and furniture (shelves, poles, coat racks, paper towel dispenser, soap dispenser, etc.)
• Upgrade: Beds, desks, wardrobes, tables, chairs, and any other removable furniture items.
-
• 2x6 walls (R21 Insulation)
• 1-hr rating for wall assemblies (allows tighter spacing between units)
• California Building Code Compliance
• Sprinkler System
• Solar system and battery backup
• Engineered temporary and permanent foundations
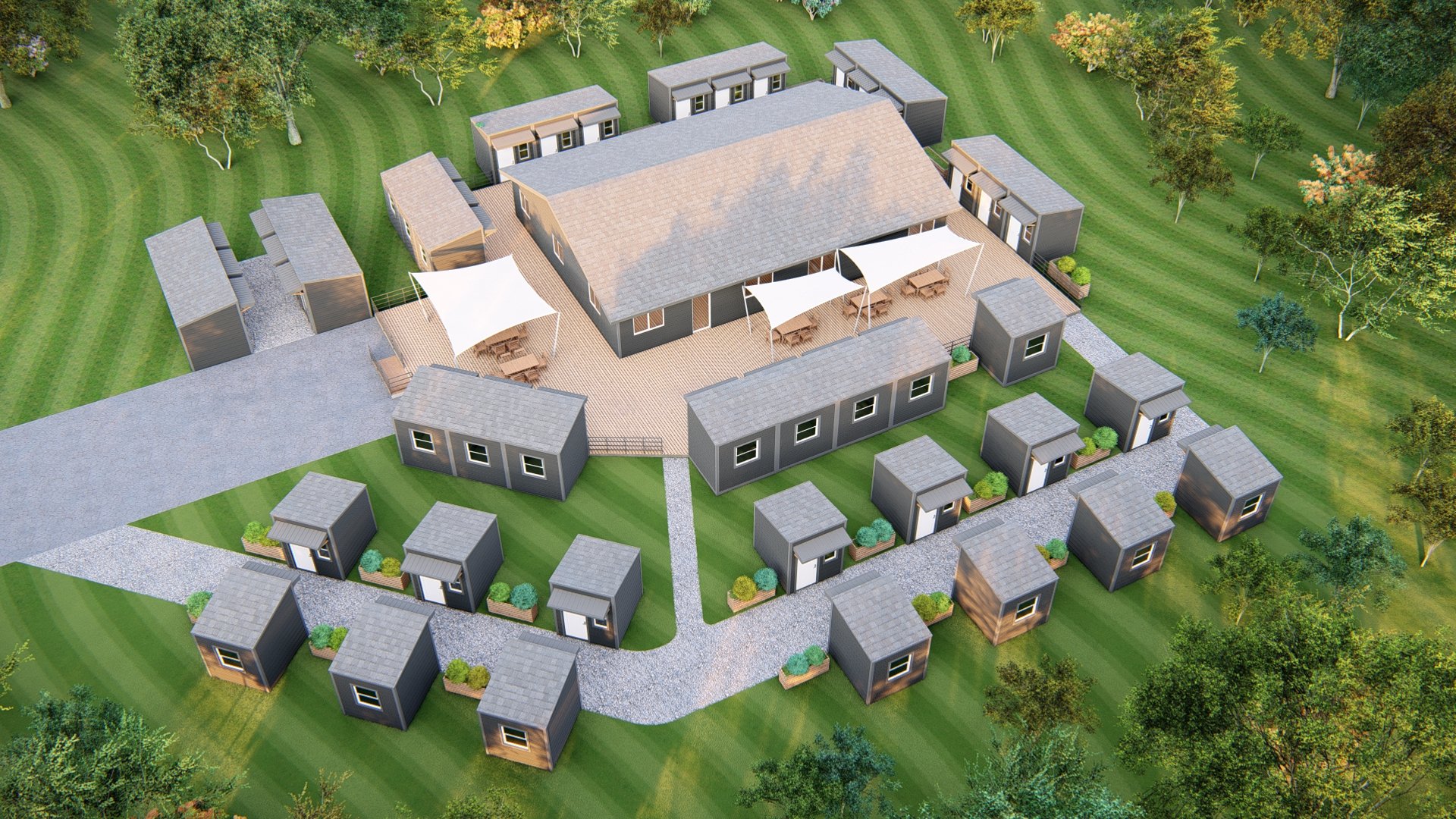
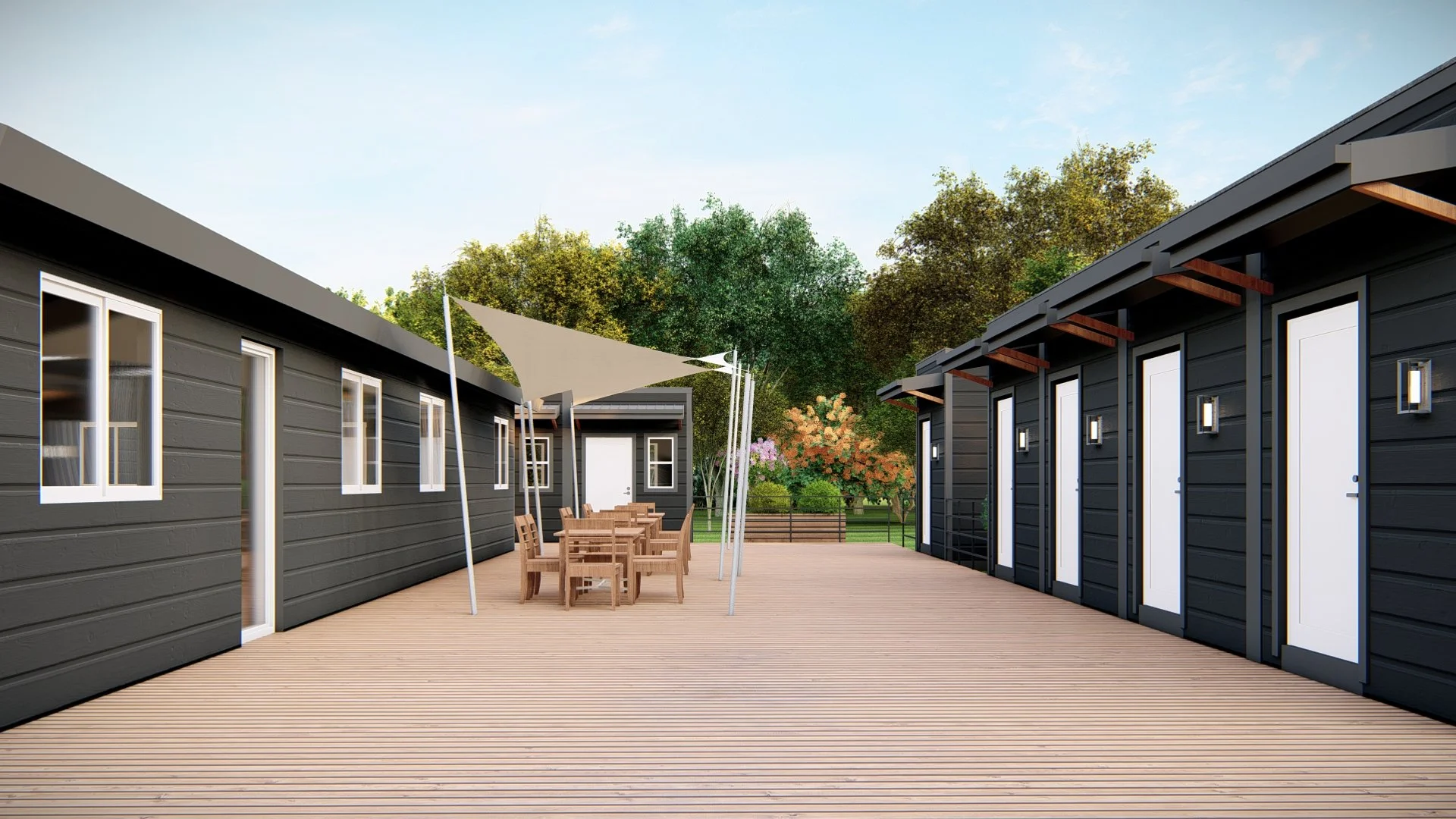

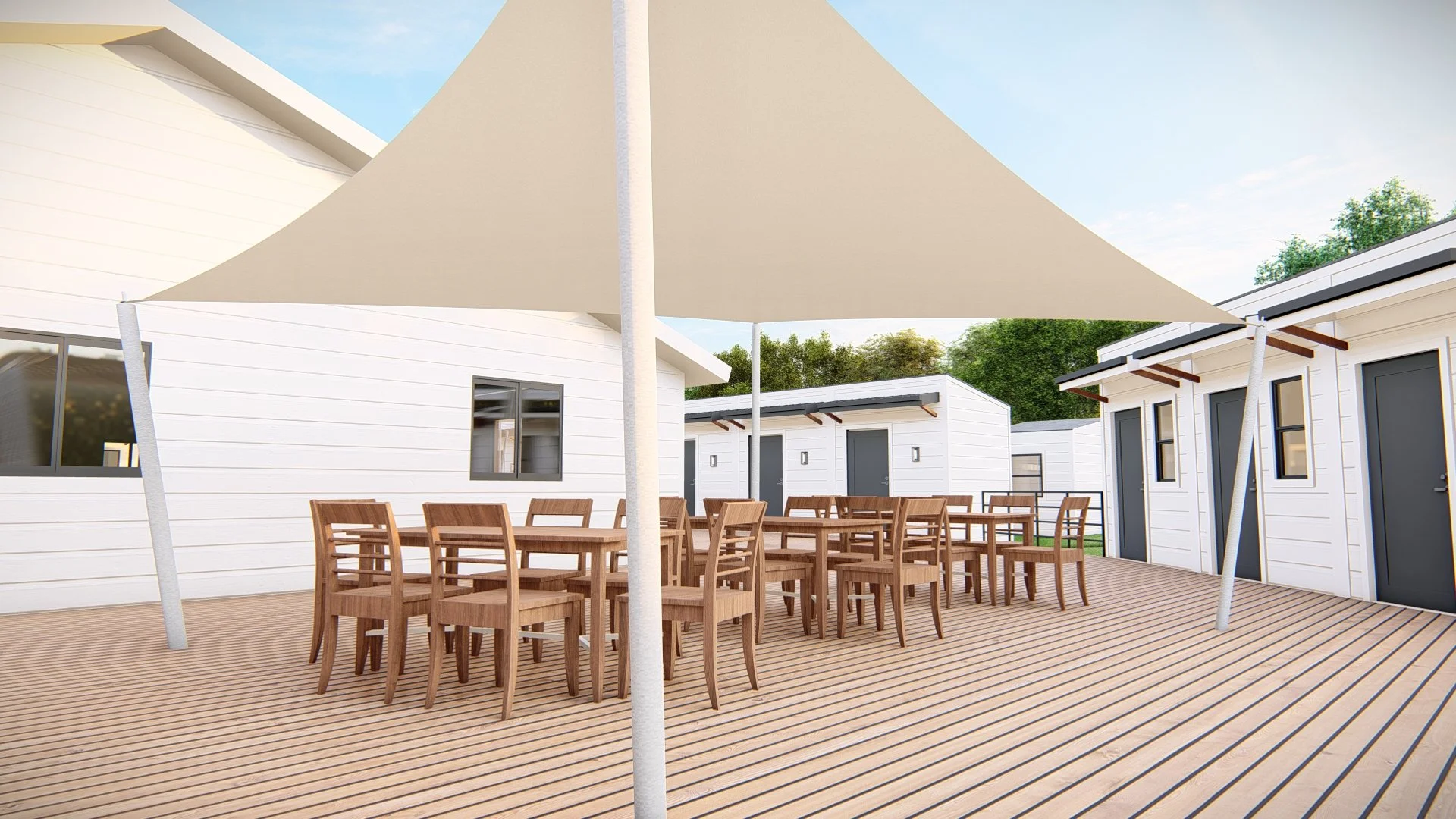
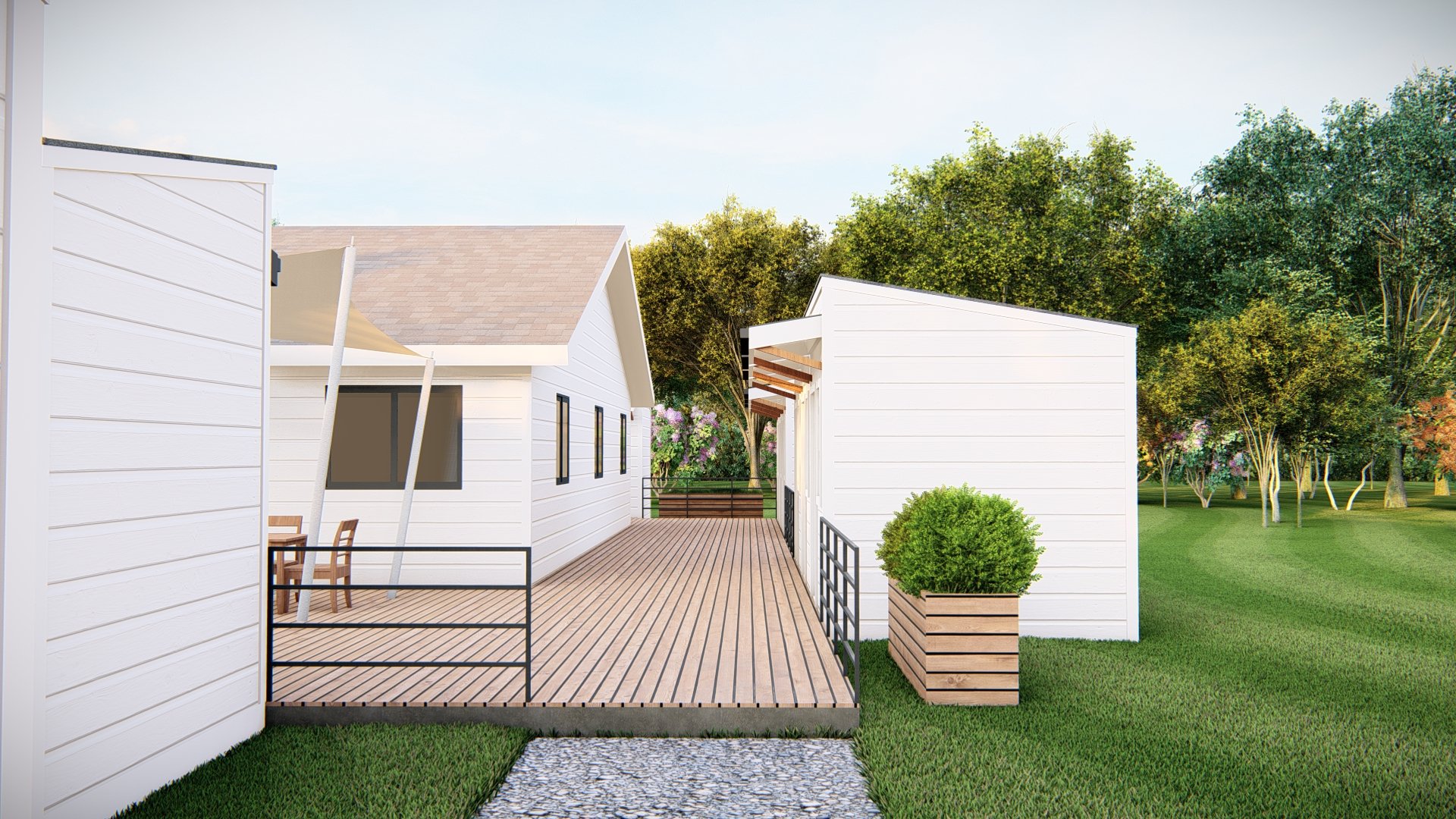
The ModOuts Building Experience
Design Build
With our strong background in the design-build approach, the ModOuts team has the ability to support the existing project team in any area needed.
Even though we offer pre-engineered solutions, we are aware that emergency shelters are new to most local jurisdictions, planning, and building departments. While Appendix P brings some clarity and guideline, it still leaves room for specific local requirements that make it challenging for standardized products to meet all specifications in regards to fire and life safety, size and accessibility.
Starting at orders over 40 shelter units, ModOuts is able to adjust it’s pre-engineered designs and configure them for the specific project requirements. This is not limited to but includes:
High Fire Hazard Severity Zone (WUI-Zone) compliance
1-hr fire ratings of exterior walls to achieve higher density
Upgrade to special snow and wind loads
combining units to larger buildings including all rated assemblies
adjusting the unit sizes, finish, furnishing, window size and placement, etc.
Manufacturing
The ModOuts Shelters are manufactured in our factory in Redding California. Our team has great experience in also building other product types like custom ADU’s, single family residences all the way to low-rise multifamily.
Transport & Lifting
Depending on the size, the units are transported using various sizes of trailers by specialized transporting contractors.
All units are designed to prioritize absolute transport efficiency for the initial transport as well as any future redeployments
Depending on the size, the units are installed with a telescopic tele-handler or a mobile crane. In most cases, the cost savings of building larger units or combining units (duplex, triplex, quadplex), offset the cost for larger install equipment.
Warranty
If the install is performed by ModOuts or approved by a ModOuts inspector, ModOuts offers a 1 year warranty on fit-and finish including cosmetic defects and a 10 year warranty on the structural system.
Permanent Install
Units are placed either on geo screw foundation or regular concrete foundation
The attachment to the foundation via the outside of the unit allows for a full California Building Code compliance as well as easy removal in case of redeployment.
Temporary Install
Most common for Appendix P projects
Works for hard surfaces (asphalt, concrete, etc.) and soft surfaces (gravel, sand, dirt, etc.)
The units are placed on pressure treated 2x dimensional lumber bearing plates in order to level out any unevenness in the underground
To achieve a California Building Code compliant foundation, the pressure treated plates can be anchored with earth screws which allow for shear transfer and resistance against uplift. For Appendix P applications, no attachment to the ground is required.
Optional Turn-Key Services
ModOuts by US-Offsite does not only design and manufacture the shelter village buildings. Due to our experience in turn-key modular construction we can include the following services into our scope:
Shipping incl. all permitting and coordination
Site-prep
Install of units (temporary or permanent)
Redeployment of units to different project site
All service requests that might occur (expansions, additions, adjustments)
All these services can be performed by ModOuts of a ModOuts expert can consult the existing project team.
Redeployment
Whether installed temporary or permanent, all our units can be uninstalled and loaded on a truck to be shipped to a storage facility or their next deployment.
If the new application requires adjustments to the units, ModOuts is able to assist with design services as well as performing construction services on-site. The use of traditional light wood frame construction is highly versatile and uncomplicated for changes and adjustments.
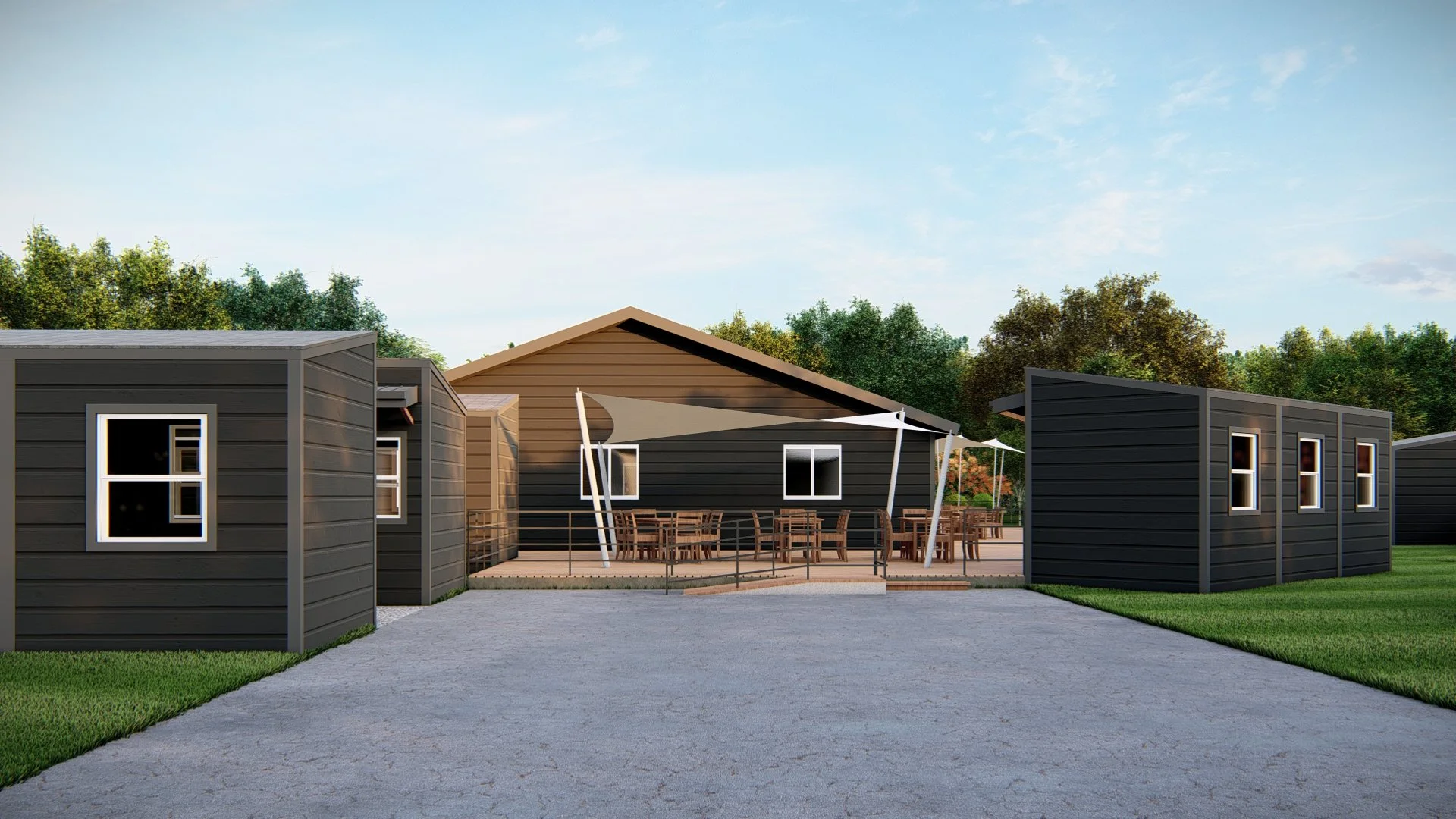
Versatility
ModOuts offers two styles:
CONTEMPORARY & CRAFTSMAN
All units can be painted in different colors to allow for a colorful and warm village experience.
Style
Contemporary
CRAFTSMAN
Color
Combinations
One of the main advantages of ModOuts is the option to combine units to a larger building.
Individual cabins offer the most privacy but can take up a large footprint.
Combining between 2 and 6 units allows for higher density while not giving up comfort due to our double insulated walls. Besides the sleeping units also bathrooms, laundry rooms and flex rooms can be combined.